Warehouse Fitout Costs in Melbourne: Our 2025 Guide
Setting up or refurbishing a warehouse is a significant endeavour that requires careful planning to optimise space, functionality, and operational efficiency. Whether you’re expanding storage capacity, enhancing logistics, or creating a multifunctional workspace, a well-executed warehouse fitout is essential for meeting your business goals effectively.
In today’s competitive market, the cost and quality of your warehouse fitout can impact productivity, safety, and overall business success. From storage solutions and infrastructure to safety considerations and regulatory compliance, every aspect requires thorough consideration to ensure a seamless fitout process.
If you’re embarking on a warehouse fitout project, whether for distribution, manufacturing, office or storage purposes, this guide is for you. We’ll explore the essential costs involved, highlight common challenges, and provide tips to help you navigate the fitout journey successfully.
Warehouse Fitout Cost Per Square Meter
Warehouse fitout costs can vary significantly depending on the size of the space, specific requirements, and the intended use of the warehouse. Most business owners can expect to pay the following:
Between $900-$1500 per sqm
Build code requirements also change significantly across industries. An exceptional fitout expert understands this and will balance all of these requirements within a reasonable budget.
Other Potential Warehouse Fitout Costs
Below are some of the more specific costs associated with warehouse fitouts. Prices can vary depending on the materials used and warehouse size. Where possible we provide price ranges with our most up-to-date costs. Keep in mind that every build is different and will have different needs.
- Pallet Racking: Essential for maximising vertical space and organising warehouse inventory. Costs for an individual 2.5-metre high unit start around $1000.
- Other Storage Solutions: For smaller items or specialised storage needs. Individual shelving unit costs can vary from $300 up to $1000.
- HVAC Systems: Heating, ventilation, and air conditioning to maintain optimal working conditions. Costs can vary depending on build complexity.
- Electrical: Upgrading electrical systems for lighting, machinery, and technology integration. Unique connections may need to be created depending on the layout of your fitout.
- Flooring: If using any part of your warehouse for food preparation, kitchen areas often require features such as stainless steel substrate and safety vinyl (compliant flooring). While substrate costs can vary by project, compliant flooring costs start at around $200 per sqm.
- Security Systems: CCTV, access control, and alarm systems to protect inventory and equipment. Installation costs vary but typically range from $1,000 to $10,000.
- Other Considerations
- Office space
- Break rooms
- Staff amenities (e.g. bathrooms, toilets and showers)
That may seem like a lot of costs to consider upfront, but every warehouse fitout is different. Industries also have their own set of building code requirements to meet. We have years of industry experience in Melbourne and know the regulations inside and out. We’ll help you get the most out of your fitout budget so you don’t get lost in the red tape of fitout construction.
If you plan to fitout your warehouse for food and commercial use – like a bar, brewery, or restaurant – check out our costs blog for more specific information about hospitality fitouts.
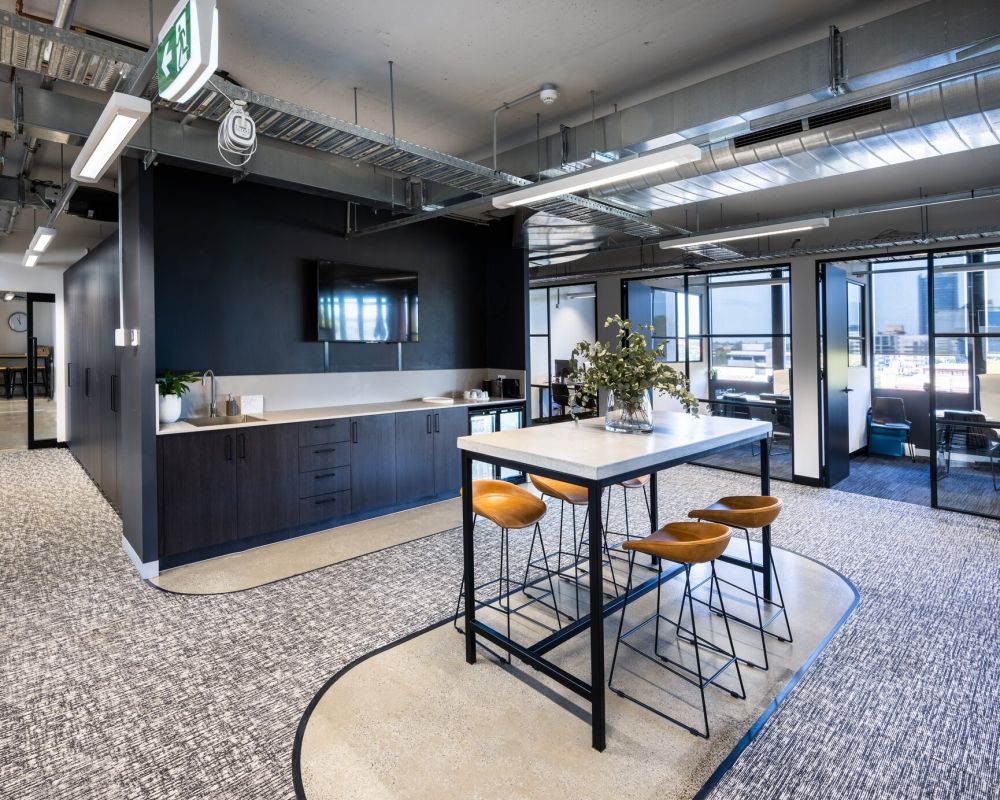
Designing Office Space in Your Warehouse Fitout
If you are planning to do a warehouse redesign, 9 times out of 10 you’ll need to fitout out an office as well. Whether you’re fitting out a logistics centre or a gym, office space is a necessary part of any location business, acting as the control centre for day-to-day operations.
Without the office, there is no clear delineation between your floor and office teams – both groups need different workplace setups for optimal productivity.
Considering this, you’ll want to create a space that looks and feels different from the rest of the warehouse; a space that feels more inviting and conducive to office work. There are additional considerations to factor into your budget, but nothing that would be out of the ordinary. These include:
- Office furniture
- Design
- Open-plan, private or hybrid?
- If private offices are created, will they be fully enclosed spaces?
- How many workstations are needed?
- Will there be a breakout space(s) for team collaboration?
- Will the office be on the ground floor or a mezzanine?
- Reception areas
- Utilities (e.g. electricity, plumbing and internet)
Recommended Reading: Fitout Costs Explained: How to Not Break the Bank on Your Office Fitout
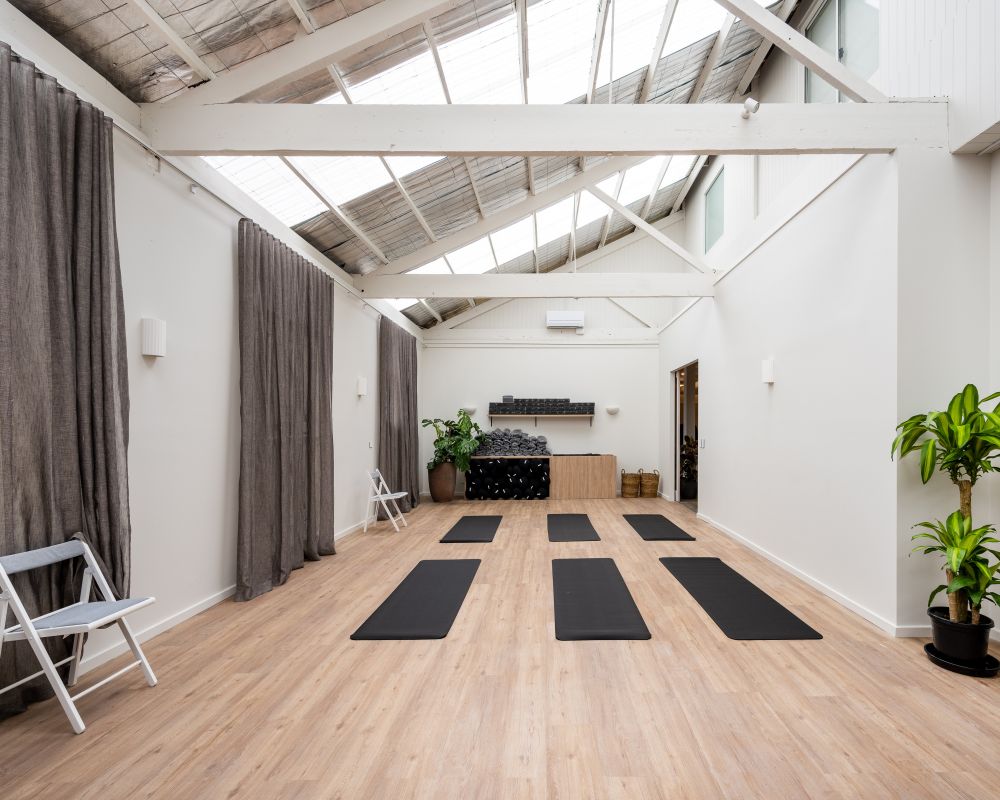
Common Warehouse Fitout Issues (and How to Avoid Them)
Now you know what to be on the lookout for, but what about those things a builder might not tell you about? Let’s explore them below.
Mezzanine Installation
Building a mezzanine inside a warehouse is a great way to optimise space, ensuring fitout longevity as your business grows. If you are considering this, we suggest engaging a structural engineer to assess the warehouse’s foundation and structural integrity. We understand that this can be a time-consuming and complicated process, especially in heritage-listed spaces. Our team can help you with this entire process.
Power
Warehouses are empty shells, giving you the freedom to design and modify as you’d like. And since these structures only come with the essentials, you may need to establish new connections for routing power throughout the entire space. Electrical tests are necessary throughout the build to ensure no outages occur after your fitout is complete.
With previous experience in this space, we’ll be upfront when assessing timeframes for power installation. Additional work is usually required to effectively distribute all the power coming into the building. Safety comes first before everything else.
Material Lead Time
Lead time for certain materials can vary. While materials can be sourced locally, some items may need to be imported. At Canopy Fitouts we take a comprehensive approach to quoting and building your fitout. We forecast lead times wherever possible, and will suggest alternatives if you desire a speedier completion.
Regulatory Bodies
With any construction project, approval from regulatory bodies will be required. Rather than taking on council fees, permit plans, and the potential red tape involved, our team will assist you and ensure the process is seamless. Don’t let neglected paperwork hold up your fitout.
Asbestos
Asbestos is the most hidden issue on this list. While it may not be an issue for your fitout, we’ll never really know until we get started on the project. At Canopy, we’ll do all early leg work to catch signs of potential asbestos and will help you get a professional to decontaminate the premises quickly.
Hidden Costs
We recommend allocating at least 30% of your budget to cover hidden services like the ones above. We will be as upfront as possible in the early stages of your build to help you avoid these costs later on.
Speak With a Warehouse Fitout Expert
At Canopy Fitouts, we specialise in providing transparent guidance and expertise throughout the warehouse fitout process. Every warehouse project is unique, and our team is dedicated to helping you achieve your operational goals efficiently and cost-effectively. If you have any specific questions or are ready to get started on your fitout, speak with our knowledgeable team today.